Coax or bifilar choke
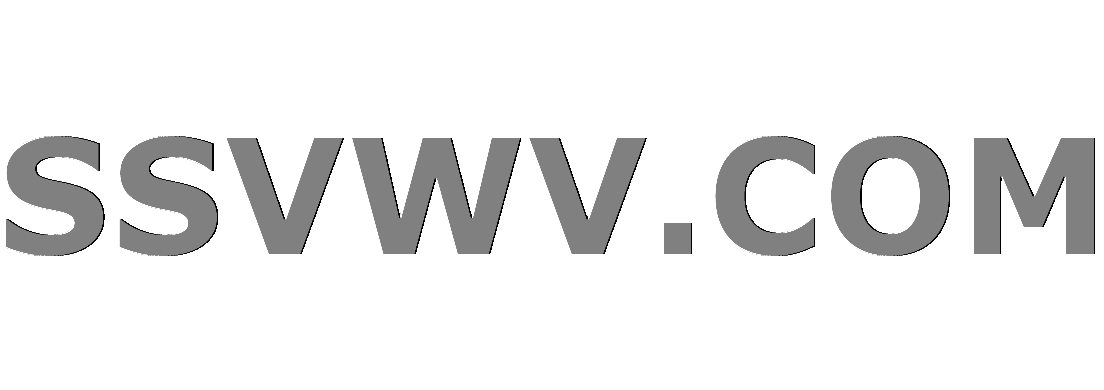
Multi tool use
$begingroup$
Making a common mode choke out of bifilar windings has proven rather difficult. For me the difficulty lies in getting the impedance to remain a constant 50 ohms from on the HF bands. I've tried 14 gauge enameled and I've tried 18 gauge PTFE. The wires seem very sensitive to any kind of change in position.
I've been modeling the choke after the one shown on this tutorial. Also what's the deal with that design? It's like someone took a 4:1 guanella and just cut the connection that makes it 4:1. Turning it into to parallel 1:1 chokes.
Is there any disadvantage to simply using coax windings instead of bifilar? Can I just wrap 11 or 12 turns of RG-316 around a toroid? How much more choking impedance do you get from a bifilar choke?
impedance balun choke-balun
$endgroup$
add a comment |
$begingroup$
Making a common mode choke out of bifilar windings has proven rather difficult. For me the difficulty lies in getting the impedance to remain a constant 50 ohms from on the HF bands. I've tried 14 gauge enameled and I've tried 18 gauge PTFE. The wires seem very sensitive to any kind of change in position.
I've been modeling the choke after the one shown on this tutorial. Also what's the deal with that design? It's like someone took a 4:1 guanella and just cut the connection that makes it 4:1. Turning it into to parallel 1:1 chokes.
Is there any disadvantage to simply using coax windings instead of bifilar? Can I just wrap 11 or 12 turns of RG-316 around a toroid? How much more choking impedance do you get from a bifilar choke?
impedance balun choke-balun
$endgroup$
add a comment |
$begingroup$
Making a common mode choke out of bifilar windings has proven rather difficult. For me the difficulty lies in getting the impedance to remain a constant 50 ohms from on the HF bands. I've tried 14 gauge enameled and I've tried 18 gauge PTFE. The wires seem very sensitive to any kind of change in position.
I've been modeling the choke after the one shown on this tutorial. Also what's the deal with that design? It's like someone took a 4:1 guanella and just cut the connection that makes it 4:1. Turning it into to parallel 1:1 chokes.
Is there any disadvantage to simply using coax windings instead of bifilar? Can I just wrap 11 or 12 turns of RG-316 around a toroid? How much more choking impedance do you get from a bifilar choke?
impedance balun choke-balun
$endgroup$
Making a common mode choke out of bifilar windings has proven rather difficult. For me the difficulty lies in getting the impedance to remain a constant 50 ohms from on the HF bands. I've tried 14 gauge enameled and I've tried 18 gauge PTFE. The wires seem very sensitive to any kind of change in position.
I've been modeling the choke after the one shown on this tutorial. Also what's the deal with that design? It's like someone took a 4:1 guanella and just cut the connection that makes it 4:1. Turning it into to parallel 1:1 chokes.
Is there any disadvantage to simply using coax windings instead of bifilar? Can I just wrap 11 or 12 turns of RG-316 around a toroid? How much more choking impedance do you get from a bifilar choke?
impedance balun choke-balun
impedance balun choke-balun
asked 4 hours ago
PaulPaul
1147
1147
add a comment |
add a comment |
2 Answers
2
active
oldest
votes
$begingroup$
In most multi-band balun applications, there is rarely a need to maintain a perfect 50 ohm impedance within the balun. The feedpoint or input impedance is varying widely so another impedance bump in the mix typically has no detrimental effect.
I highly recommend the use of coaxial wound over bifilar style for a 1:1 balun. Comparatively, the coaxial and bifilar design can be made to have equivalent common mode choking.
The bifilar style will couple some of the energy traveling on the parallel lines into the core - much like getting a parallel transmission line too close to metal objects. This creates an unnecessary loss and it promotes heating of the core due to the complex permeability of the core material.
It is also very difficult to fabricate a true bifilar 50 ohm line. The design is so touchy that even minor changes in the wire coating thickness or failure to keep the lines adjacent will cause impedance discontinuities. Due to this marginal construction, the voltage withstand rating of this type of transmission line is much lower than what can be attained through the application of a coaxial transmission line.
The coaxial wound style will keep all but the common mode current from creating a flux in the core. This is the ideal behavior of a transmission line transformer of this type. Do estimate the losses in this length of transmission line in order to project the effect on core heating. If heating of the core due to coax loss is a design constraint, consider using higher impedance coaxial cable (e.g. 75 ohm) as this will reduce the loss compared to the same size/class of 50 ohm cable.
Selection of the correct core material is essential. Generally, type 31 is suitable for the lower HF bands and type 43 for the upper HF bands. Look at the complex permeability curves and use a material where the $mu$''s is greater than $mu$'s for the frequencies of interest.
You may find some practical information regarding the number of turns of coax vs the core material on the G3TXQ (now an SK) site. Here are some examples of his analysis:
The K9YC 2018 Cookbook also features type 31 material balun designs.
$endgroup$
$begingroup$
Jim has a new PDF revised in 2019, linked to in my comment above.
$endgroup$
– Mike Waters♦
4 hours ago
$begingroup$
@MikeWaters Thanks, Mike but in your link, chapter 7 is not included. My link is his referenced chapter 7 contents specific to choking baluns.
$endgroup$
– Glenn W9IQ
4 hours ago
$begingroup$
Yours was the correct one. From Jim: "I no longer recommend coax wound through multiple cores. I'ts simply not practical to wind chokes that way and get anything close to the same result every time -- turns must go through the core in the same order, a scrambled turn cancels a turn, turn diameter matters a lot, and so on. ...
$endgroup$
– Mike Waters♦
4 hours ago
$begingroup$
"... The new cookbook uses RG400, 12-2 Teflon/silver pairs, or 12/2 THHN or NM pairs, all tightly wound around a single core. There are recommendations for chokes in series to increase power handling. There is also data for the new 4-in o.d. supersized toroids, which are great for 160M. k9yc.com/2018Cookbook.pdf"
$endgroup$
– Mike Waters♦
4 hours ago
$begingroup$
Feel free to incorporate this into your answer, which was emailed to me by Jim (who gave me permission to share it).
$endgroup$
– Mike Waters♦
4 hours ago
|
show 1 more comment
$begingroup$
The advantage of using coax for a 1:1 choke-balun is the constant Z0 of 50 ohms. As can be seen in the following graphs, the only time a 1:1 choke-balun accomplishes a 1:1 transformation is when it sees 50 ohms at its output. Any other impedance at the output causes an impedance transformation because the SWR is not 1:1.
$endgroup$
add a comment |
Your Answer
StackExchange.ifUsing("editor", function () {
return StackExchange.using("mathjaxEditing", function () {
StackExchange.MarkdownEditor.creationCallbacks.add(function (editor, postfix) {
StackExchange.mathjaxEditing.prepareWmdForMathJax(editor, postfix, [["$", "$"], ["\\(","\\)"]]);
});
});
}, "mathjax-editing");
StackExchange.ifUsing("editor", function () {
return StackExchange.using("schematics", function () {
StackExchange.schematics.init();
});
}, "cicuitlab");
StackExchange.ready(function() {
var channelOptions = {
tags: "".split(" "),
id: "520"
};
initTagRenderer("".split(" "), "".split(" "), channelOptions);
StackExchange.using("externalEditor", function() {
// Have to fire editor after snippets, if snippets enabled
if (StackExchange.settings.snippets.snippetsEnabled) {
StackExchange.using("snippets", function() {
createEditor();
});
}
else {
createEditor();
}
});
function createEditor() {
StackExchange.prepareEditor({
heartbeatType: 'answer',
autoActivateHeartbeat: false,
convertImagesToLinks: false,
noModals: true,
showLowRepImageUploadWarning: true,
reputationToPostImages: null,
bindNavPrevention: true,
postfix: "",
imageUploader: {
brandingHtml: "Powered by u003ca class="icon-imgur-white" href="https://imgur.com/"u003eu003c/au003e",
contentPolicyHtml: "User contributions licensed under u003ca href="https://creativecommons.org/licenses/by-sa/3.0/"u003ecc by-sa 3.0 with attribution requiredu003c/au003e u003ca href="https://stackoverflow.com/legal/content-policy"u003e(content policy)u003c/au003e",
allowUrls: true
},
noCode: true, onDemand: true,
discardSelector: ".discard-answer"
,immediatelyShowMarkdownHelp:true
});
}
});
Sign up or log in
StackExchange.ready(function () {
StackExchange.helpers.onClickDraftSave('#login-link');
});
Sign up using Google
Sign up using Facebook
Sign up using Email and Password
Post as a guest
Required, but never shown
StackExchange.ready(
function () {
StackExchange.openid.initPostLogin('.new-post-login', 'https%3a%2f%2fham.stackexchange.com%2fquestions%2f13005%2fcoax-or-bifilar-choke%23new-answer', 'question_page');
}
);
Post as a guest
Required, but never shown
2 Answers
2
active
oldest
votes
2 Answers
2
active
oldest
votes
active
oldest
votes
active
oldest
votes
$begingroup$
In most multi-band balun applications, there is rarely a need to maintain a perfect 50 ohm impedance within the balun. The feedpoint or input impedance is varying widely so another impedance bump in the mix typically has no detrimental effect.
I highly recommend the use of coaxial wound over bifilar style for a 1:1 balun. Comparatively, the coaxial and bifilar design can be made to have equivalent common mode choking.
The bifilar style will couple some of the energy traveling on the parallel lines into the core - much like getting a parallel transmission line too close to metal objects. This creates an unnecessary loss and it promotes heating of the core due to the complex permeability of the core material.
It is also very difficult to fabricate a true bifilar 50 ohm line. The design is so touchy that even minor changes in the wire coating thickness or failure to keep the lines adjacent will cause impedance discontinuities. Due to this marginal construction, the voltage withstand rating of this type of transmission line is much lower than what can be attained through the application of a coaxial transmission line.
The coaxial wound style will keep all but the common mode current from creating a flux in the core. This is the ideal behavior of a transmission line transformer of this type. Do estimate the losses in this length of transmission line in order to project the effect on core heating. If heating of the core due to coax loss is a design constraint, consider using higher impedance coaxial cable (e.g. 75 ohm) as this will reduce the loss compared to the same size/class of 50 ohm cable.
Selection of the correct core material is essential. Generally, type 31 is suitable for the lower HF bands and type 43 for the upper HF bands. Look at the complex permeability curves and use a material where the $mu$''s is greater than $mu$'s for the frequencies of interest.
You may find some practical information regarding the number of turns of coax vs the core material on the G3TXQ (now an SK) site. Here are some examples of his analysis:
The K9YC 2018 Cookbook also features type 31 material balun designs.
$endgroup$
$begingroup$
Jim has a new PDF revised in 2019, linked to in my comment above.
$endgroup$
– Mike Waters♦
4 hours ago
$begingroup$
@MikeWaters Thanks, Mike but in your link, chapter 7 is not included. My link is his referenced chapter 7 contents specific to choking baluns.
$endgroup$
– Glenn W9IQ
4 hours ago
$begingroup$
Yours was the correct one. From Jim: "I no longer recommend coax wound through multiple cores. I'ts simply not practical to wind chokes that way and get anything close to the same result every time -- turns must go through the core in the same order, a scrambled turn cancels a turn, turn diameter matters a lot, and so on. ...
$endgroup$
– Mike Waters♦
4 hours ago
$begingroup$
"... The new cookbook uses RG400, 12-2 Teflon/silver pairs, or 12/2 THHN or NM pairs, all tightly wound around a single core. There are recommendations for chokes in series to increase power handling. There is also data for the new 4-in o.d. supersized toroids, which are great for 160M. k9yc.com/2018Cookbook.pdf"
$endgroup$
– Mike Waters♦
4 hours ago
$begingroup$
Feel free to incorporate this into your answer, which was emailed to me by Jim (who gave me permission to share it).
$endgroup$
– Mike Waters♦
4 hours ago
|
show 1 more comment
$begingroup$
In most multi-band balun applications, there is rarely a need to maintain a perfect 50 ohm impedance within the balun. The feedpoint or input impedance is varying widely so another impedance bump in the mix typically has no detrimental effect.
I highly recommend the use of coaxial wound over bifilar style for a 1:1 balun. Comparatively, the coaxial and bifilar design can be made to have equivalent common mode choking.
The bifilar style will couple some of the energy traveling on the parallel lines into the core - much like getting a parallel transmission line too close to metal objects. This creates an unnecessary loss and it promotes heating of the core due to the complex permeability of the core material.
It is also very difficult to fabricate a true bifilar 50 ohm line. The design is so touchy that even minor changes in the wire coating thickness or failure to keep the lines adjacent will cause impedance discontinuities. Due to this marginal construction, the voltage withstand rating of this type of transmission line is much lower than what can be attained through the application of a coaxial transmission line.
The coaxial wound style will keep all but the common mode current from creating a flux in the core. This is the ideal behavior of a transmission line transformer of this type. Do estimate the losses in this length of transmission line in order to project the effect on core heating. If heating of the core due to coax loss is a design constraint, consider using higher impedance coaxial cable (e.g. 75 ohm) as this will reduce the loss compared to the same size/class of 50 ohm cable.
Selection of the correct core material is essential. Generally, type 31 is suitable for the lower HF bands and type 43 for the upper HF bands. Look at the complex permeability curves and use a material where the $mu$''s is greater than $mu$'s for the frequencies of interest.
You may find some practical information regarding the number of turns of coax vs the core material on the G3TXQ (now an SK) site. Here are some examples of his analysis:
The K9YC 2018 Cookbook also features type 31 material balun designs.
$endgroup$
$begingroup$
Jim has a new PDF revised in 2019, linked to in my comment above.
$endgroup$
– Mike Waters♦
4 hours ago
$begingroup$
@MikeWaters Thanks, Mike but in your link, chapter 7 is not included. My link is his referenced chapter 7 contents specific to choking baluns.
$endgroup$
– Glenn W9IQ
4 hours ago
$begingroup$
Yours was the correct one. From Jim: "I no longer recommend coax wound through multiple cores. I'ts simply not practical to wind chokes that way and get anything close to the same result every time -- turns must go through the core in the same order, a scrambled turn cancels a turn, turn diameter matters a lot, and so on. ...
$endgroup$
– Mike Waters♦
4 hours ago
$begingroup$
"... The new cookbook uses RG400, 12-2 Teflon/silver pairs, or 12/2 THHN or NM pairs, all tightly wound around a single core. There are recommendations for chokes in series to increase power handling. There is also data for the new 4-in o.d. supersized toroids, which are great for 160M. k9yc.com/2018Cookbook.pdf"
$endgroup$
– Mike Waters♦
4 hours ago
$begingroup$
Feel free to incorporate this into your answer, which was emailed to me by Jim (who gave me permission to share it).
$endgroup$
– Mike Waters♦
4 hours ago
|
show 1 more comment
$begingroup$
In most multi-band balun applications, there is rarely a need to maintain a perfect 50 ohm impedance within the balun. The feedpoint or input impedance is varying widely so another impedance bump in the mix typically has no detrimental effect.
I highly recommend the use of coaxial wound over bifilar style for a 1:1 balun. Comparatively, the coaxial and bifilar design can be made to have equivalent common mode choking.
The bifilar style will couple some of the energy traveling on the parallel lines into the core - much like getting a parallel transmission line too close to metal objects. This creates an unnecessary loss and it promotes heating of the core due to the complex permeability of the core material.
It is also very difficult to fabricate a true bifilar 50 ohm line. The design is so touchy that even minor changes in the wire coating thickness or failure to keep the lines adjacent will cause impedance discontinuities. Due to this marginal construction, the voltage withstand rating of this type of transmission line is much lower than what can be attained through the application of a coaxial transmission line.
The coaxial wound style will keep all but the common mode current from creating a flux in the core. This is the ideal behavior of a transmission line transformer of this type. Do estimate the losses in this length of transmission line in order to project the effect on core heating. If heating of the core due to coax loss is a design constraint, consider using higher impedance coaxial cable (e.g. 75 ohm) as this will reduce the loss compared to the same size/class of 50 ohm cable.
Selection of the correct core material is essential. Generally, type 31 is suitable for the lower HF bands and type 43 for the upper HF bands. Look at the complex permeability curves and use a material where the $mu$''s is greater than $mu$'s for the frequencies of interest.
You may find some practical information regarding the number of turns of coax vs the core material on the G3TXQ (now an SK) site. Here are some examples of his analysis:
The K9YC 2018 Cookbook also features type 31 material balun designs.
$endgroup$
In most multi-band balun applications, there is rarely a need to maintain a perfect 50 ohm impedance within the balun. The feedpoint or input impedance is varying widely so another impedance bump in the mix typically has no detrimental effect.
I highly recommend the use of coaxial wound over bifilar style for a 1:1 balun. Comparatively, the coaxial and bifilar design can be made to have equivalent common mode choking.
The bifilar style will couple some of the energy traveling on the parallel lines into the core - much like getting a parallel transmission line too close to metal objects. This creates an unnecessary loss and it promotes heating of the core due to the complex permeability of the core material.
It is also very difficult to fabricate a true bifilar 50 ohm line. The design is so touchy that even minor changes in the wire coating thickness or failure to keep the lines adjacent will cause impedance discontinuities. Due to this marginal construction, the voltage withstand rating of this type of transmission line is much lower than what can be attained through the application of a coaxial transmission line.
The coaxial wound style will keep all but the common mode current from creating a flux in the core. This is the ideal behavior of a transmission line transformer of this type. Do estimate the losses in this length of transmission line in order to project the effect on core heating. If heating of the core due to coax loss is a design constraint, consider using higher impedance coaxial cable (e.g. 75 ohm) as this will reduce the loss compared to the same size/class of 50 ohm cable.
Selection of the correct core material is essential. Generally, type 31 is suitable for the lower HF bands and type 43 for the upper HF bands. Look at the complex permeability curves and use a material where the $mu$''s is greater than $mu$'s for the frequencies of interest.
You may find some practical information regarding the number of turns of coax vs the core material on the G3TXQ (now an SK) site. Here are some examples of his analysis:
The K9YC 2018 Cookbook also features type 31 material balun designs.
edited 2 hours ago
answered 4 hours ago


Glenn W9IQGlenn W9IQ
16.5k11146
16.5k11146
$begingroup$
Jim has a new PDF revised in 2019, linked to in my comment above.
$endgroup$
– Mike Waters♦
4 hours ago
$begingroup$
@MikeWaters Thanks, Mike but in your link, chapter 7 is not included. My link is his referenced chapter 7 contents specific to choking baluns.
$endgroup$
– Glenn W9IQ
4 hours ago
$begingroup$
Yours was the correct one. From Jim: "I no longer recommend coax wound through multiple cores. I'ts simply not practical to wind chokes that way and get anything close to the same result every time -- turns must go through the core in the same order, a scrambled turn cancels a turn, turn diameter matters a lot, and so on. ...
$endgroup$
– Mike Waters♦
4 hours ago
$begingroup$
"... The new cookbook uses RG400, 12-2 Teflon/silver pairs, or 12/2 THHN or NM pairs, all tightly wound around a single core. There are recommendations for chokes in series to increase power handling. There is also data for the new 4-in o.d. supersized toroids, which are great for 160M. k9yc.com/2018Cookbook.pdf"
$endgroup$
– Mike Waters♦
4 hours ago
$begingroup$
Feel free to incorporate this into your answer, which was emailed to me by Jim (who gave me permission to share it).
$endgroup$
– Mike Waters♦
4 hours ago
|
show 1 more comment
$begingroup$
Jim has a new PDF revised in 2019, linked to in my comment above.
$endgroup$
– Mike Waters♦
4 hours ago
$begingroup$
@MikeWaters Thanks, Mike but in your link, chapter 7 is not included. My link is his referenced chapter 7 contents specific to choking baluns.
$endgroup$
– Glenn W9IQ
4 hours ago
$begingroup$
Yours was the correct one. From Jim: "I no longer recommend coax wound through multiple cores. I'ts simply not practical to wind chokes that way and get anything close to the same result every time -- turns must go through the core in the same order, a scrambled turn cancels a turn, turn diameter matters a lot, and so on. ...
$endgroup$
– Mike Waters♦
4 hours ago
$begingroup$
"... The new cookbook uses RG400, 12-2 Teflon/silver pairs, or 12/2 THHN or NM pairs, all tightly wound around a single core. There are recommendations for chokes in series to increase power handling. There is also data for the new 4-in o.d. supersized toroids, which are great for 160M. k9yc.com/2018Cookbook.pdf"
$endgroup$
– Mike Waters♦
4 hours ago
$begingroup$
Feel free to incorporate this into your answer, which was emailed to me by Jim (who gave me permission to share it).
$endgroup$
– Mike Waters♦
4 hours ago
$begingroup$
Jim has a new PDF revised in 2019, linked to in my comment above.
$endgroup$
– Mike Waters♦
4 hours ago
$begingroup$
Jim has a new PDF revised in 2019, linked to in my comment above.
$endgroup$
– Mike Waters♦
4 hours ago
$begingroup$
@MikeWaters Thanks, Mike but in your link, chapter 7 is not included. My link is his referenced chapter 7 contents specific to choking baluns.
$endgroup$
– Glenn W9IQ
4 hours ago
$begingroup$
@MikeWaters Thanks, Mike but in your link, chapter 7 is not included. My link is his referenced chapter 7 contents specific to choking baluns.
$endgroup$
– Glenn W9IQ
4 hours ago
$begingroup$
Yours was the correct one. From Jim: "I no longer recommend coax wound through multiple cores. I'ts simply not practical to wind chokes that way and get anything close to the same result every time -- turns must go through the core in the same order, a scrambled turn cancels a turn, turn diameter matters a lot, and so on. ...
$endgroup$
– Mike Waters♦
4 hours ago
$begingroup$
Yours was the correct one. From Jim: "I no longer recommend coax wound through multiple cores. I'ts simply not practical to wind chokes that way and get anything close to the same result every time -- turns must go through the core in the same order, a scrambled turn cancels a turn, turn diameter matters a lot, and so on. ...
$endgroup$
– Mike Waters♦
4 hours ago
$begingroup$
"... The new cookbook uses RG400, 12-2 Teflon/silver pairs, or 12/2 THHN or NM pairs, all tightly wound around a single core. There are recommendations for chokes in series to increase power handling. There is also data for the new 4-in o.d. supersized toroids, which are great for 160M. k9yc.com/2018Cookbook.pdf"
$endgroup$
– Mike Waters♦
4 hours ago
$begingroup$
"... The new cookbook uses RG400, 12-2 Teflon/silver pairs, or 12/2 THHN or NM pairs, all tightly wound around a single core. There are recommendations for chokes in series to increase power handling. There is also data for the new 4-in o.d. supersized toroids, which are great for 160M. k9yc.com/2018Cookbook.pdf"
$endgroup$
– Mike Waters♦
4 hours ago
$begingroup$
Feel free to incorporate this into your answer, which was emailed to me by Jim (who gave me permission to share it).
$endgroup$
– Mike Waters♦
4 hours ago
$begingroup$
Feel free to incorporate this into your answer, which was emailed to me by Jim (who gave me permission to share it).
$endgroup$
– Mike Waters♦
4 hours ago
|
show 1 more comment
$begingroup$
The advantage of using coax for a 1:1 choke-balun is the constant Z0 of 50 ohms. As can be seen in the following graphs, the only time a 1:1 choke-balun accomplishes a 1:1 transformation is when it sees 50 ohms at its output. Any other impedance at the output causes an impedance transformation because the SWR is not 1:1.
$endgroup$
add a comment |
$begingroup$
The advantage of using coax for a 1:1 choke-balun is the constant Z0 of 50 ohms. As can be seen in the following graphs, the only time a 1:1 choke-balun accomplishes a 1:1 transformation is when it sees 50 ohms at its output. Any other impedance at the output causes an impedance transformation because the SWR is not 1:1.
$endgroup$
add a comment |
$begingroup$
The advantage of using coax for a 1:1 choke-balun is the constant Z0 of 50 ohms. As can be seen in the following graphs, the only time a 1:1 choke-balun accomplishes a 1:1 transformation is when it sees 50 ohms at its output. Any other impedance at the output causes an impedance transformation because the SWR is not 1:1.
$endgroup$
The advantage of using coax for a 1:1 choke-balun is the constant Z0 of 50 ohms. As can be seen in the following graphs, the only time a 1:1 choke-balun accomplishes a 1:1 transformation is when it sees 50 ohms at its output. Any other impedance at the output causes an impedance transformation because the SWR is not 1:1.
answered 1 hour ago


Cecil - W5DXPCecil - W5DXP
76516
76516
add a comment |
add a comment |
Thanks for contributing an answer to Amateur Radio Stack Exchange!
- Please be sure to answer the question. Provide details and share your research!
But avoid …
- Asking for help, clarification, or responding to other answers.
- Making statements based on opinion; back them up with references or personal experience.
Use MathJax to format equations. MathJax reference.
To learn more, see our tips on writing great answers.
Sign up or log in
StackExchange.ready(function () {
StackExchange.helpers.onClickDraftSave('#login-link');
});
Sign up using Google
Sign up using Facebook
Sign up using Email and Password
Post as a guest
Required, but never shown
StackExchange.ready(
function () {
StackExchange.openid.initPostLogin('.new-post-login', 'https%3a%2f%2fham.stackexchange.com%2fquestions%2f13005%2fcoax-or-bifilar-choke%23new-answer', 'question_page');
}
);
Post as a guest
Required, but never shown
Sign up or log in
StackExchange.ready(function () {
StackExchange.helpers.onClickDraftSave('#login-link');
});
Sign up using Google
Sign up using Facebook
Sign up using Email and Password
Post as a guest
Required, but never shown
Sign up or log in
StackExchange.ready(function () {
StackExchange.helpers.onClickDraftSave('#login-link');
});
Sign up using Google
Sign up using Facebook
Sign up using Email and Password
Post as a guest
Required, but never shown
Sign up or log in
StackExchange.ready(function () {
StackExchange.helpers.onClickDraftSave('#login-link');
});
Sign up using Google
Sign up using Facebook
Sign up using Email and Password
Sign up using Google
Sign up using Facebook
Sign up using Email and Password
Post as a guest
Required, but never shown
Required, but never shown
Required, but never shown
Required, but never shown
Required, but never shown
Required, but never shown
Required, but never shown
Required, but never shown
Required, but never shown
QJIkrsge3U 8xRkBYcBfw0W,fS5X3gMNTxI7M2OWJB Xlv,FEel,oLeEpHEpVt,dju,vsFNZR8C yyus,sr