Is micro rebar a better way to reinforce concrete than rebar?
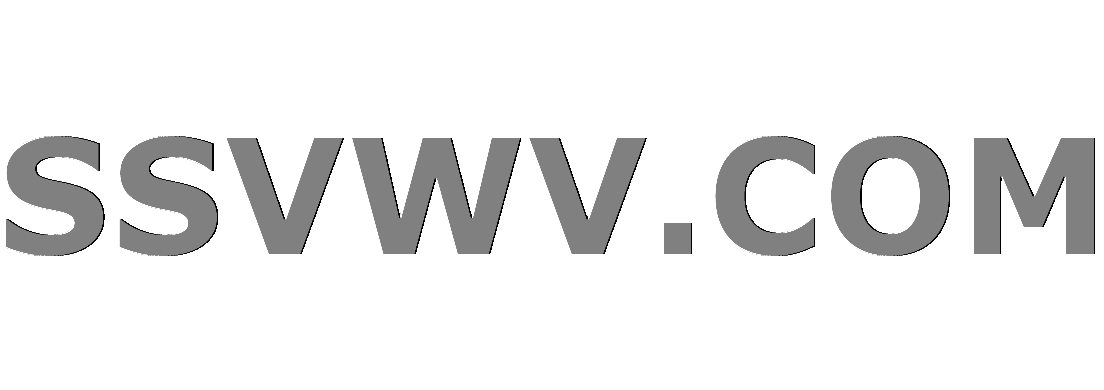
Multi tool use
This site claims that the small wires(twisted steel micro rebar) they created are a good replacement to a typical rebar concrete reinforcement if not even better.
a reinforcement technology that could product provide quantifiably
better resiliency, ductility and elasticity to concrete structures.
It's hard to believe that the small wires could replace long continuous rebars. Their product have been around since 2003 and if that's true what they claim how come I still mostly see the typical long reinforcement bars used on the construction sites? Shouldn't this be mostly used everywhere by now? It doesn't seem to be more expensive and also it is less labor demanding.
technology construction
add a comment |
This site claims that the small wires(twisted steel micro rebar) they created are a good replacement to a typical rebar concrete reinforcement if not even better.
a reinforcement technology that could product provide quantifiably
better resiliency, ductility and elasticity to concrete structures.
It's hard to believe that the small wires could replace long continuous rebars. Their product have been around since 2003 and if that's true what they claim how come I still mostly see the typical long reinforcement bars used on the construction sites? Shouldn't this be mostly used everywhere by now? It doesn't seem to be more expensive and also it is less labor demanding.
technology construction
Further article on the subject: concreteconstruction.net/how-to/materials/… . This is from a concrete industry publication, so perhaps read it skeptically. It claims projects using this type of material since the 1960s and cites a variety of pros/cons.
– DaveInCaz
Mar 30 at 1:13
add a comment |
This site claims that the small wires(twisted steel micro rebar) they created are a good replacement to a typical rebar concrete reinforcement if not even better.
a reinforcement technology that could product provide quantifiably
better resiliency, ductility and elasticity to concrete structures.
It's hard to believe that the small wires could replace long continuous rebars. Their product have been around since 2003 and if that's true what they claim how come I still mostly see the typical long reinforcement bars used on the construction sites? Shouldn't this be mostly used everywhere by now? It doesn't seem to be more expensive and also it is less labor demanding.
technology construction
This site claims that the small wires(twisted steel micro rebar) they created are a good replacement to a typical rebar concrete reinforcement if not even better.
a reinforcement technology that could product provide quantifiably
better resiliency, ductility and elasticity to concrete structures.
It's hard to believe that the small wires could replace long continuous rebars. Their product have been around since 2003 and if that's true what they claim how come I still mostly see the typical long reinforcement bars used on the construction sites? Shouldn't this be mostly used everywhere by now? It doesn't seem to be more expensive and also it is less labor demanding.
technology construction
technology construction
asked Mar 29 at 14:11
GrasperGrasper
1,22611121
1,22611121
Further article on the subject: concreteconstruction.net/how-to/materials/… . This is from a concrete industry publication, so perhaps read it skeptically. It claims projects using this type of material since the 1960s and cites a variety of pros/cons.
– DaveInCaz
Mar 30 at 1:13
add a comment |
Further article on the subject: concreteconstruction.net/how-to/materials/… . This is from a concrete industry publication, so perhaps read it skeptically. It claims projects using this type of material since the 1960s and cites a variety of pros/cons.
– DaveInCaz
Mar 30 at 1:13
Further article on the subject: concreteconstruction.net/how-to/materials/… . This is from a concrete industry publication, so perhaps read it skeptically. It claims projects using this type of material since the 1960s and cites a variety of pros/cons.
– DaveInCaz
Mar 30 at 1:13
Further article on the subject: concreteconstruction.net/how-to/materials/… . This is from a concrete industry publication, so perhaps read it skeptically. It claims projects using this type of material since the 1960s and cites a variety of pros/cons.
– DaveInCaz
Mar 30 at 1:13
add a comment |
2 Answers
2
active
oldest
votes
The question headline seems to be slightly misinterpreting the company's claims
Carefully rereading their claims, I realized they do not specify what Twisted Steel Micro Reinforcement (TSMR) reinforced concrete is better than. On a quick read, I just assumed they meant it is better than rebar reinforced concrete, because that is what the pictures imply, but it is never explicitly stated.
Helix Steel’s TSMR increases concrete’s strength and resilience and eliminates or reduces traditional reinforcement (rebar and mesh) required by building codes.
This sentence implies that traditional rebar reinforcement is still required in some cases; TSMR is not better than just rebar in all cases.
Helix's Science
Their publications page presents 3 conference papers, two technical reports, and an industry magazine article. I have skimmed through these and found experimental comparisons between plain concrete (not reinforced) and the twisted helix reinforced concrete. I could only find one comparison between rebar reinforced concrete and the helix reinforced concrete, and that related to the explosive test that their pictures show. No quantitative results were presented from that test, just the pictures.
It is worth noting that their best evidence is published as conference papers, which typically face a lower standard of peer review than journal articles. This is definitely a better standard of evidence than I see from many marketing teams, but it isn't the highest standard of evidence.
It is worth noting that helix's product can be used in things like road pavement, where rebar reinforcement is not an option. It can also be used in combination with traditional rebar reinforcement.
Conclusion
From their evidence and a careful read of their claims, TSMR reinforced concrete is definitely stronger than plain concrete. If it is combined with traditional rebar, it can be stronger than rebar alone. Helix does not claim that it will ever replace traditional rebar completely.
2
Literally: show me the codze that state TSMR is acceptable to use in lieu of rebar. Even if it does, it still leaves you open to liability if you decide to use a product from 2003 instead of a proven one from the 15th century.
– Mazura
Mar 30 at 1:10
@Mazura FYI, rebar reinforced concrete only started to show up in the 19th century. Rebar reinforcement was being used in other ways from 15th century onwards; but using it in concrete didn't begin until later.
– JMac
Apr 1 at 16:09
add a comment |
This is just a form of steel fibre reinforced concrete (SFRC) with twisted fibers. SFRC in general has been around since 1874. It's also been heavily research for at least 50 years (previous source and the last in this answer say this.)
Twisted fibers are slightly better than other kinds in some respects, but not by much. (There's no point in getting into details on this here.)
As for replacing rebar, a more introductory 2018 academic presentation, which is aware of twisted fibers (has photos among the showcased types), has these general points about SFRC in general:
- The addition of fibres enhances the structural performance of plain concrete (much higher fracture energy)
- Fibres reduce the crack spacing and crack width, thereby improving serviceability and durability
- Currently used SFRC mixes exhibit a softening behaviour in tension and cannot fully replace conventional reinforcement
- Hybrid reinforcement (fibres and conventional reinforcing bars) can be used, but may affect ductility
So, SFRC is clearly not a replacement for rebar in general. And these bits are also relevant:
Several causes are preventing a more widespread use of SFRC:
Lack of standardised design procedures and material test procedures
High fibre contents (e.g. 1.5% = 120 kg/m3) as required for structural applications (and used in many experiments) are causing severe problems in terms of mixing and workability of concrete mix
With common fibre contents (e.g. 0.5% = 40 kg/m3), the tensile strength of concrete cannot be matched at cracking
Since this is written by a (Swiss) professor (ETH Zürich) in this field, I'd be amazed if he hadn't hear of some amazing breakthrough in this respect (in particular for products already commercialized.)
And if that's not enough, he repeats again:
For general application in engineering practice, it is necessary to
include conventional reinforcement in combination with SFRC to
ensure structural safety and an adequate crack distribution.
As for the table in Dave's answer, which is for a certain application (footings) it comes with this preamble:
For residential footings the International Residential Code (IRC-2015) section R403 describes the use of plain concrete
footings provided that the concrete will be in compression. However, it is customary to provide reinforcement to
minimize cracking and hold tight any cracks that occur due to drying shrinkage and/or differential temperature effects.
It's only in this optional role that they provide a replacement table. This actually not too surprising. The ETH presentation does mention (and has some pictures) of bridge deck overlays done with SFRC variants; it has a photo (and schematic) example of the Viaduc de Chillon (a bridge in Switzerland).
The same presentation does have one example of "more structural" SFRC-based bridge girders from Dura (a Malaysian company). These do indeed do away with most conventional reinforcements, according to the manufacturer:
DURA® UBG eliminate the used of conventional steel reinforcing bars and stirrups, except at regions where jointing detail are required for composite construction. All steel fibers used are made from high carbon steel wires with tensile strength of minimum 2300 MPa.
Due to the absence of conventional steel reinforcements, DURA® girders can be designed and produced in much slenderer and efficient sections, with no concern for classical issues such as minimum concrete cover, to prevent corrosion of steel reinforcement;
And they have been used in practice:
3rd December 2010 marks the history calendar of engineering in Malaysia as it is the date of the launching of Malaysia’s first ever Ultra-High Performance ‘ductile’ Concrete (UHPdC) bridge girder. This record breaking 50 m single span motorway bridge girder produced and designed by Dura Technology S/B and Perunding Faisal, Abraham dan Augustin S/B holds the marvel of engineering. To date, this bridge girder is considered as the world longest single-span prestressed UHPdC bridge girder for motorway application. The previous record was at 48 m in Japan.
The girders look like this:
(The rebar sticking out is for the aforementioned "jointing detail".)
They have a schematic where this joniting rebar is present and where not (alas it's low resolution):
"High fibre contents (e.g. 1.5% = 120 kg/m3) as required for structural applications (and used in many experiments) are causing severe problems in terms of mixing and workability of concrete mix would" add to the cost of laying a lot and the total cost.
– user2617804
Mar 31 at 2:30
add a comment |
2 Answers
2
active
oldest
votes
2 Answers
2
active
oldest
votes
active
oldest
votes
active
oldest
votes
The question headline seems to be slightly misinterpreting the company's claims
Carefully rereading their claims, I realized they do not specify what Twisted Steel Micro Reinforcement (TSMR) reinforced concrete is better than. On a quick read, I just assumed they meant it is better than rebar reinforced concrete, because that is what the pictures imply, but it is never explicitly stated.
Helix Steel’s TSMR increases concrete’s strength and resilience and eliminates or reduces traditional reinforcement (rebar and mesh) required by building codes.
This sentence implies that traditional rebar reinforcement is still required in some cases; TSMR is not better than just rebar in all cases.
Helix's Science
Their publications page presents 3 conference papers, two technical reports, and an industry magazine article. I have skimmed through these and found experimental comparisons between plain concrete (not reinforced) and the twisted helix reinforced concrete. I could only find one comparison between rebar reinforced concrete and the helix reinforced concrete, and that related to the explosive test that their pictures show. No quantitative results were presented from that test, just the pictures.
It is worth noting that their best evidence is published as conference papers, which typically face a lower standard of peer review than journal articles. This is definitely a better standard of evidence than I see from many marketing teams, but it isn't the highest standard of evidence.
It is worth noting that helix's product can be used in things like road pavement, where rebar reinforcement is not an option. It can also be used in combination with traditional rebar reinforcement.
Conclusion
From their evidence and a careful read of their claims, TSMR reinforced concrete is definitely stronger than plain concrete. If it is combined with traditional rebar, it can be stronger than rebar alone. Helix does not claim that it will ever replace traditional rebar completely.
2
Literally: show me the codze that state TSMR is acceptable to use in lieu of rebar. Even if it does, it still leaves you open to liability if you decide to use a product from 2003 instead of a proven one from the 15th century.
– Mazura
Mar 30 at 1:10
@Mazura FYI, rebar reinforced concrete only started to show up in the 19th century. Rebar reinforcement was being used in other ways from 15th century onwards; but using it in concrete didn't begin until later.
– JMac
Apr 1 at 16:09
add a comment |
The question headline seems to be slightly misinterpreting the company's claims
Carefully rereading their claims, I realized they do not specify what Twisted Steel Micro Reinforcement (TSMR) reinforced concrete is better than. On a quick read, I just assumed they meant it is better than rebar reinforced concrete, because that is what the pictures imply, but it is never explicitly stated.
Helix Steel’s TSMR increases concrete’s strength and resilience and eliminates or reduces traditional reinforcement (rebar and mesh) required by building codes.
This sentence implies that traditional rebar reinforcement is still required in some cases; TSMR is not better than just rebar in all cases.
Helix's Science
Their publications page presents 3 conference papers, two technical reports, and an industry magazine article. I have skimmed through these and found experimental comparisons between plain concrete (not reinforced) and the twisted helix reinforced concrete. I could only find one comparison between rebar reinforced concrete and the helix reinforced concrete, and that related to the explosive test that their pictures show. No quantitative results were presented from that test, just the pictures.
It is worth noting that their best evidence is published as conference papers, which typically face a lower standard of peer review than journal articles. This is definitely a better standard of evidence than I see from many marketing teams, but it isn't the highest standard of evidence.
It is worth noting that helix's product can be used in things like road pavement, where rebar reinforcement is not an option. It can also be used in combination with traditional rebar reinforcement.
Conclusion
From their evidence and a careful read of their claims, TSMR reinforced concrete is definitely stronger than plain concrete. If it is combined with traditional rebar, it can be stronger than rebar alone. Helix does not claim that it will ever replace traditional rebar completely.
2
Literally: show me the codze that state TSMR is acceptable to use in lieu of rebar. Even if it does, it still leaves you open to liability if you decide to use a product from 2003 instead of a proven one from the 15th century.
– Mazura
Mar 30 at 1:10
@Mazura FYI, rebar reinforced concrete only started to show up in the 19th century. Rebar reinforcement was being used in other ways from 15th century onwards; but using it in concrete didn't begin until later.
– JMac
Apr 1 at 16:09
add a comment |
The question headline seems to be slightly misinterpreting the company's claims
Carefully rereading their claims, I realized they do not specify what Twisted Steel Micro Reinforcement (TSMR) reinforced concrete is better than. On a quick read, I just assumed they meant it is better than rebar reinforced concrete, because that is what the pictures imply, but it is never explicitly stated.
Helix Steel’s TSMR increases concrete’s strength and resilience and eliminates or reduces traditional reinforcement (rebar and mesh) required by building codes.
This sentence implies that traditional rebar reinforcement is still required in some cases; TSMR is not better than just rebar in all cases.
Helix's Science
Their publications page presents 3 conference papers, two technical reports, and an industry magazine article. I have skimmed through these and found experimental comparisons between plain concrete (not reinforced) and the twisted helix reinforced concrete. I could only find one comparison between rebar reinforced concrete and the helix reinforced concrete, and that related to the explosive test that their pictures show. No quantitative results were presented from that test, just the pictures.
It is worth noting that their best evidence is published as conference papers, which typically face a lower standard of peer review than journal articles. This is definitely a better standard of evidence than I see from many marketing teams, but it isn't the highest standard of evidence.
It is worth noting that helix's product can be used in things like road pavement, where rebar reinforcement is not an option. It can also be used in combination with traditional rebar reinforcement.
Conclusion
From their evidence and a careful read of their claims, TSMR reinforced concrete is definitely stronger than plain concrete. If it is combined with traditional rebar, it can be stronger than rebar alone. Helix does not claim that it will ever replace traditional rebar completely.
The question headline seems to be slightly misinterpreting the company's claims
Carefully rereading their claims, I realized they do not specify what Twisted Steel Micro Reinforcement (TSMR) reinforced concrete is better than. On a quick read, I just assumed they meant it is better than rebar reinforced concrete, because that is what the pictures imply, but it is never explicitly stated.
Helix Steel’s TSMR increases concrete’s strength and resilience and eliminates or reduces traditional reinforcement (rebar and mesh) required by building codes.
This sentence implies that traditional rebar reinforcement is still required in some cases; TSMR is not better than just rebar in all cases.
Helix's Science
Their publications page presents 3 conference papers, two technical reports, and an industry magazine article. I have skimmed through these and found experimental comparisons between plain concrete (not reinforced) and the twisted helix reinforced concrete. I could only find one comparison between rebar reinforced concrete and the helix reinforced concrete, and that related to the explosive test that their pictures show. No quantitative results were presented from that test, just the pictures.
It is worth noting that their best evidence is published as conference papers, which typically face a lower standard of peer review than journal articles. This is definitely a better standard of evidence than I see from many marketing teams, but it isn't the highest standard of evidence.
It is worth noting that helix's product can be used in things like road pavement, where rebar reinforcement is not an option. It can also be used in combination with traditional rebar reinforcement.
Conclusion
From their evidence and a careful read of their claims, TSMR reinforced concrete is definitely stronger than plain concrete. If it is combined with traditional rebar, it can be stronger than rebar alone. Helix does not claim that it will ever replace traditional rebar completely.
edited Mar 29 at 17:12
answered Mar 29 at 15:53
BobTheAverageBobTheAverage
10.4k62941
10.4k62941
2
Literally: show me the codze that state TSMR is acceptable to use in lieu of rebar. Even if it does, it still leaves you open to liability if you decide to use a product from 2003 instead of a proven one from the 15th century.
– Mazura
Mar 30 at 1:10
@Mazura FYI, rebar reinforced concrete only started to show up in the 19th century. Rebar reinforcement was being used in other ways from 15th century onwards; but using it in concrete didn't begin until later.
– JMac
Apr 1 at 16:09
add a comment |
2
Literally: show me the codze that state TSMR is acceptable to use in lieu of rebar. Even if it does, it still leaves you open to liability if you decide to use a product from 2003 instead of a proven one from the 15th century.
– Mazura
Mar 30 at 1:10
@Mazura FYI, rebar reinforced concrete only started to show up in the 19th century. Rebar reinforcement was being used in other ways from 15th century onwards; but using it in concrete didn't begin until later.
– JMac
Apr 1 at 16:09
2
2
Literally: show me the codze that state TSMR is acceptable to use in lieu of rebar. Even if it does, it still leaves you open to liability if you decide to use a product from 2003 instead of a proven one from the 15th century.
– Mazura
Mar 30 at 1:10
Literally: show me the codze that state TSMR is acceptable to use in lieu of rebar. Even if it does, it still leaves you open to liability if you decide to use a product from 2003 instead of a proven one from the 15th century.
– Mazura
Mar 30 at 1:10
@Mazura FYI, rebar reinforced concrete only started to show up in the 19th century. Rebar reinforcement was being used in other ways from 15th century onwards; but using it in concrete didn't begin until later.
– JMac
Apr 1 at 16:09
@Mazura FYI, rebar reinforced concrete only started to show up in the 19th century. Rebar reinforcement was being used in other ways from 15th century onwards; but using it in concrete didn't begin until later.
– JMac
Apr 1 at 16:09
add a comment |
This is just a form of steel fibre reinforced concrete (SFRC) with twisted fibers. SFRC in general has been around since 1874. It's also been heavily research for at least 50 years (previous source and the last in this answer say this.)
Twisted fibers are slightly better than other kinds in some respects, but not by much. (There's no point in getting into details on this here.)
As for replacing rebar, a more introductory 2018 academic presentation, which is aware of twisted fibers (has photos among the showcased types), has these general points about SFRC in general:
- The addition of fibres enhances the structural performance of plain concrete (much higher fracture energy)
- Fibres reduce the crack spacing and crack width, thereby improving serviceability and durability
- Currently used SFRC mixes exhibit a softening behaviour in tension and cannot fully replace conventional reinforcement
- Hybrid reinforcement (fibres and conventional reinforcing bars) can be used, but may affect ductility
So, SFRC is clearly not a replacement for rebar in general. And these bits are also relevant:
Several causes are preventing a more widespread use of SFRC:
Lack of standardised design procedures and material test procedures
High fibre contents (e.g. 1.5% = 120 kg/m3) as required for structural applications (and used in many experiments) are causing severe problems in terms of mixing and workability of concrete mix
With common fibre contents (e.g. 0.5% = 40 kg/m3), the tensile strength of concrete cannot be matched at cracking
Since this is written by a (Swiss) professor (ETH Zürich) in this field, I'd be amazed if he hadn't hear of some amazing breakthrough in this respect (in particular for products already commercialized.)
And if that's not enough, he repeats again:
For general application in engineering practice, it is necessary to
include conventional reinforcement in combination with SFRC to
ensure structural safety and an adequate crack distribution.
As for the table in Dave's answer, which is for a certain application (footings) it comes with this preamble:
For residential footings the International Residential Code (IRC-2015) section R403 describes the use of plain concrete
footings provided that the concrete will be in compression. However, it is customary to provide reinforcement to
minimize cracking and hold tight any cracks that occur due to drying shrinkage and/or differential temperature effects.
It's only in this optional role that they provide a replacement table. This actually not too surprising. The ETH presentation does mention (and has some pictures) of bridge deck overlays done with SFRC variants; it has a photo (and schematic) example of the Viaduc de Chillon (a bridge in Switzerland).
The same presentation does have one example of "more structural" SFRC-based bridge girders from Dura (a Malaysian company). These do indeed do away with most conventional reinforcements, according to the manufacturer:
DURA® UBG eliminate the used of conventional steel reinforcing bars and stirrups, except at regions where jointing detail are required for composite construction. All steel fibers used are made from high carbon steel wires with tensile strength of minimum 2300 MPa.
Due to the absence of conventional steel reinforcements, DURA® girders can be designed and produced in much slenderer and efficient sections, with no concern for classical issues such as minimum concrete cover, to prevent corrosion of steel reinforcement;
And they have been used in practice:
3rd December 2010 marks the history calendar of engineering in Malaysia as it is the date of the launching of Malaysia’s first ever Ultra-High Performance ‘ductile’ Concrete (UHPdC) bridge girder. This record breaking 50 m single span motorway bridge girder produced and designed by Dura Technology S/B and Perunding Faisal, Abraham dan Augustin S/B holds the marvel of engineering. To date, this bridge girder is considered as the world longest single-span prestressed UHPdC bridge girder for motorway application. The previous record was at 48 m in Japan.
The girders look like this:
(The rebar sticking out is for the aforementioned "jointing detail".)
They have a schematic where this joniting rebar is present and where not (alas it's low resolution):
"High fibre contents (e.g. 1.5% = 120 kg/m3) as required for structural applications (and used in many experiments) are causing severe problems in terms of mixing and workability of concrete mix would" add to the cost of laying a lot and the total cost.
– user2617804
Mar 31 at 2:30
add a comment |
This is just a form of steel fibre reinforced concrete (SFRC) with twisted fibers. SFRC in general has been around since 1874. It's also been heavily research for at least 50 years (previous source and the last in this answer say this.)
Twisted fibers are slightly better than other kinds in some respects, but not by much. (There's no point in getting into details on this here.)
As for replacing rebar, a more introductory 2018 academic presentation, which is aware of twisted fibers (has photos among the showcased types), has these general points about SFRC in general:
- The addition of fibres enhances the structural performance of plain concrete (much higher fracture energy)
- Fibres reduce the crack spacing and crack width, thereby improving serviceability and durability
- Currently used SFRC mixes exhibit a softening behaviour in tension and cannot fully replace conventional reinforcement
- Hybrid reinforcement (fibres and conventional reinforcing bars) can be used, but may affect ductility
So, SFRC is clearly not a replacement for rebar in general. And these bits are also relevant:
Several causes are preventing a more widespread use of SFRC:
Lack of standardised design procedures and material test procedures
High fibre contents (e.g. 1.5% = 120 kg/m3) as required for structural applications (and used in many experiments) are causing severe problems in terms of mixing and workability of concrete mix
With common fibre contents (e.g. 0.5% = 40 kg/m3), the tensile strength of concrete cannot be matched at cracking
Since this is written by a (Swiss) professor (ETH Zürich) in this field, I'd be amazed if he hadn't hear of some amazing breakthrough in this respect (in particular for products already commercialized.)
And if that's not enough, he repeats again:
For general application in engineering practice, it is necessary to
include conventional reinforcement in combination with SFRC to
ensure structural safety and an adequate crack distribution.
As for the table in Dave's answer, which is for a certain application (footings) it comes with this preamble:
For residential footings the International Residential Code (IRC-2015) section R403 describes the use of plain concrete
footings provided that the concrete will be in compression. However, it is customary to provide reinforcement to
minimize cracking and hold tight any cracks that occur due to drying shrinkage and/or differential temperature effects.
It's only in this optional role that they provide a replacement table. This actually not too surprising. The ETH presentation does mention (and has some pictures) of bridge deck overlays done with SFRC variants; it has a photo (and schematic) example of the Viaduc de Chillon (a bridge in Switzerland).
The same presentation does have one example of "more structural" SFRC-based bridge girders from Dura (a Malaysian company). These do indeed do away with most conventional reinforcements, according to the manufacturer:
DURA® UBG eliminate the used of conventional steel reinforcing bars and stirrups, except at regions where jointing detail are required for composite construction. All steel fibers used are made from high carbon steel wires with tensile strength of minimum 2300 MPa.
Due to the absence of conventional steel reinforcements, DURA® girders can be designed and produced in much slenderer and efficient sections, with no concern for classical issues such as minimum concrete cover, to prevent corrosion of steel reinforcement;
And they have been used in practice:
3rd December 2010 marks the history calendar of engineering in Malaysia as it is the date of the launching of Malaysia’s first ever Ultra-High Performance ‘ductile’ Concrete (UHPdC) bridge girder. This record breaking 50 m single span motorway bridge girder produced and designed by Dura Technology S/B and Perunding Faisal, Abraham dan Augustin S/B holds the marvel of engineering. To date, this bridge girder is considered as the world longest single-span prestressed UHPdC bridge girder for motorway application. The previous record was at 48 m in Japan.
The girders look like this:
(The rebar sticking out is for the aforementioned "jointing detail".)
They have a schematic where this joniting rebar is present and where not (alas it's low resolution):
"High fibre contents (e.g. 1.5% = 120 kg/m3) as required for structural applications (and used in many experiments) are causing severe problems in terms of mixing and workability of concrete mix would" add to the cost of laying a lot and the total cost.
– user2617804
Mar 31 at 2:30
add a comment |
This is just a form of steel fibre reinforced concrete (SFRC) with twisted fibers. SFRC in general has been around since 1874. It's also been heavily research for at least 50 years (previous source and the last in this answer say this.)
Twisted fibers are slightly better than other kinds in some respects, but not by much. (There's no point in getting into details on this here.)
As for replacing rebar, a more introductory 2018 academic presentation, which is aware of twisted fibers (has photos among the showcased types), has these general points about SFRC in general:
- The addition of fibres enhances the structural performance of plain concrete (much higher fracture energy)
- Fibres reduce the crack spacing and crack width, thereby improving serviceability and durability
- Currently used SFRC mixes exhibit a softening behaviour in tension and cannot fully replace conventional reinforcement
- Hybrid reinforcement (fibres and conventional reinforcing bars) can be used, but may affect ductility
So, SFRC is clearly not a replacement for rebar in general. And these bits are also relevant:
Several causes are preventing a more widespread use of SFRC:
Lack of standardised design procedures and material test procedures
High fibre contents (e.g. 1.5% = 120 kg/m3) as required for structural applications (and used in many experiments) are causing severe problems in terms of mixing and workability of concrete mix
With common fibre contents (e.g. 0.5% = 40 kg/m3), the tensile strength of concrete cannot be matched at cracking
Since this is written by a (Swiss) professor (ETH Zürich) in this field, I'd be amazed if he hadn't hear of some amazing breakthrough in this respect (in particular for products already commercialized.)
And if that's not enough, he repeats again:
For general application in engineering practice, it is necessary to
include conventional reinforcement in combination with SFRC to
ensure structural safety and an adequate crack distribution.
As for the table in Dave's answer, which is for a certain application (footings) it comes with this preamble:
For residential footings the International Residential Code (IRC-2015) section R403 describes the use of plain concrete
footings provided that the concrete will be in compression. However, it is customary to provide reinforcement to
minimize cracking and hold tight any cracks that occur due to drying shrinkage and/or differential temperature effects.
It's only in this optional role that they provide a replacement table. This actually not too surprising. The ETH presentation does mention (and has some pictures) of bridge deck overlays done with SFRC variants; it has a photo (and schematic) example of the Viaduc de Chillon (a bridge in Switzerland).
The same presentation does have one example of "more structural" SFRC-based bridge girders from Dura (a Malaysian company). These do indeed do away with most conventional reinforcements, according to the manufacturer:
DURA® UBG eliminate the used of conventional steel reinforcing bars and stirrups, except at regions where jointing detail are required for composite construction. All steel fibers used are made from high carbon steel wires with tensile strength of minimum 2300 MPa.
Due to the absence of conventional steel reinforcements, DURA® girders can be designed and produced in much slenderer and efficient sections, with no concern for classical issues such as minimum concrete cover, to prevent corrosion of steel reinforcement;
And they have been used in practice:
3rd December 2010 marks the history calendar of engineering in Malaysia as it is the date of the launching of Malaysia’s first ever Ultra-High Performance ‘ductile’ Concrete (UHPdC) bridge girder. This record breaking 50 m single span motorway bridge girder produced and designed by Dura Technology S/B and Perunding Faisal, Abraham dan Augustin S/B holds the marvel of engineering. To date, this bridge girder is considered as the world longest single-span prestressed UHPdC bridge girder for motorway application. The previous record was at 48 m in Japan.
The girders look like this:
(The rebar sticking out is for the aforementioned "jointing detail".)
They have a schematic where this joniting rebar is present and where not (alas it's low resolution):
This is just a form of steel fibre reinforced concrete (SFRC) with twisted fibers. SFRC in general has been around since 1874. It's also been heavily research for at least 50 years (previous source and the last in this answer say this.)
Twisted fibers are slightly better than other kinds in some respects, but not by much. (There's no point in getting into details on this here.)
As for replacing rebar, a more introductory 2018 academic presentation, which is aware of twisted fibers (has photos among the showcased types), has these general points about SFRC in general:
- The addition of fibres enhances the structural performance of plain concrete (much higher fracture energy)
- Fibres reduce the crack spacing and crack width, thereby improving serviceability and durability
- Currently used SFRC mixes exhibit a softening behaviour in tension and cannot fully replace conventional reinforcement
- Hybrid reinforcement (fibres and conventional reinforcing bars) can be used, but may affect ductility
So, SFRC is clearly not a replacement for rebar in general. And these bits are also relevant:
Several causes are preventing a more widespread use of SFRC:
Lack of standardised design procedures and material test procedures
High fibre contents (e.g. 1.5% = 120 kg/m3) as required for structural applications (and used in many experiments) are causing severe problems in terms of mixing and workability of concrete mix
With common fibre contents (e.g. 0.5% = 40 kg/m3), the tensile strength of concrete cannot be matched at cracking
Since this is written by a (Swiss) professor (ETH Zürich) in this field, I'd be amazed if he hadn't hear of some amazing breakthrough in this respect (in particular for products already commercialized.)
And if that's not enough, he repeats again:
For general application in engineering practice, it is necessary to
include conventional reinforcement in combination with SFRC to
ensure structural safety and an adequate crack distribution.
As for the table in Dave's answer, which is for a certain application (footings) it comes with this preamble:
For residential footings the International Residential Code (IRC-2015) section R403 describes the use of plain concrete
footings provided that the concrete will be in compression. However, it is customary to provide reinforcement to
minimize cracking and hold tight any cracks that occur due to drying shrinkage and/or differential temperature effects.
It's only in this optional role that they provide a replacement table. This actually not too surprising. The ETH presentation does mention (and has some pictures) of bridge deck overlays done with SFRC variants; it has a photo (and schematic) example of the Viaduc de Chillon (a bridge in Switzerland).
The same presentation does have one example of "more structural" SFRC-based bridge girders from Dura (a Malaysian company). These do indeed do away with most conventional reinforcements, according to the manufacturer:
DURA® UBG eliminate the used of conventional steel reinforcing bars and stirrups, except at regions where jointing detail are required for composite construction. All steel fibers used are made from high carbon steel wires with tensile strength of minimum 2300 MPa.
Due to the absence of conventional steel reinforcements, DURA® girders can be designed and produced in much slenderer and efficient sections, with no concern for classical issues such as minimum concrete cover, to prevent corrosion of steel reinforcement;
And they have been used in practice:
3rd December 2010 marks the history calendar of engineering in Malaysia as it is the date of the launching of Malaysia’s first ever Ultra-High Performance ‘ductile’ Concrete (UHPdC) bridge girder. This record breaking 50 m single span motorway bridge girder produced and designed by Dura Technology S/B and Perunding Faisal, Abraham dan Augustin S/B holds the marvel of engineering. To date, this bridge girder is considered as the world longest single-span prestressed UHPdC bridge girder for motorway application. The previous record was at 48 m in Japan.
The girders look like this:
(The rebar sticking out is for the aforementioned "jointing detail".)
They have a schematic where this joniting rebar is present and where not (alas it's low resolution):
edited 2 days ago
answered Mar 30 at 16:47


FizzFizz
9,59413576
9,59413576
"High fibre contents (e.g. 1.5% = 120 kg/m3) as required for structural applications (and used in many experiments) are causing severe problems in terms of mixing and workability of concrete mix would" add to the cost of laying a lot and the total cost.
– user2617804
Mar 31 at 2:30
add a comment |
"High fibre contents (e.g. 1.5% = 120 kg/m3) as required for structural applications (and used in many experiments) are causing severe problems in terms of mixing and workability of concrete mix would" add to the cost of laying a lot and the total cost.
– user2617804
Mar 31 at 2:30
"High fibre contents (e.g. 1.5% = 120 kg/m3) as required for structural applications (and used in many experiments) are causing severe problems in terms of mixing and workability of concrete mix would" add to the cost of laying a lot and the total cost.
– user2617804
Mar 31 at 2:30
"High fibre contents (e.g. 1.5% = 120 kg/m3) as required for structural applications (and used in many experiments) are causing severe problems in terms of mixing and workability of concrete mix would" add to the cost of laying a lot and the total cost.
– user2617804
Mar 31 at 2:30
add a comment |
dl,JRr,8,Y1ey ZDQ f6CVV39A,0by7O,iI0z0h0 H,hZYqw7Ko 0PiVcQyWF45GeZ,owtbk7 lOx87 c,7 p,sjPsoXeLFwy0q
Further article on the subject: concreteconstruction.net/how-to/materials/… . This is from a concrete industry publication, so perhaps read it skeptically. It claims projects using this type of material since the 1960s and cites a variety of pros/cons.
– DaveInCaz
Mar 30 at 1:13